Workforce Safety
Strengthening our culture and relationships
Every leader, employee and contractor at Devon is expected to actively participate in making Devon a safe place to work. Our values guide us to do what’s right, manage risk, stop work, and support and empower each other to stay safe. We empower our team by providing comprehensive resources to help them work safely and measuring indicators to drive improvement. Setting corporate safety goals and incorporating safety metrics into our compensation focuses everyone at Devon on the actions that will make us safer.
We’re committed to integrating the guiding principles in our Environmental, Health and Safety (EHS) Philosophy into all decisions that affect our operations. Compliance with applicable safety laws, regulations, policies and protocols is one of these principles, and we reinforce it in our Code of Business Conduct and Ethics, EHS Policy and safety orientation, training and engagements.
Our governance structure supports Devon’s commitment to making safety our top priority. The Governance, Environmental and Public Policy (GEPP) Committee of our board of directors reviews our safety policies and performance and keeps the full board informed. Devon’s executive vice president and chief operating officer (COO) is responsible for our safety performance. Our vice president of EHS and measurement reports to the COO on EHS strategy, activities and disclosures.
Devon senior leaders oversee safety policy and performance, with support from the EHS Council. In turn, our workforce is empowered to take the necessary time and actions to perform work safely and stop work if they see a safety risk.
Setting safety and health strategy
To drive continuous improvement, the Devon EHS Council, comprising of EHS and operational managers, sets safety and health strategy, helps ensure implementation and tracks the company’s safety performance. The council meets regularly to monitor performance, share lessons learned and engage in roundtable discussions to keep the organization updated on stakeholder expectations for EHS performance.
Contractor management is a key component of the EHS Council’s roadmap and our EHS Management System. Because contractors perform the majority of Devon’s work in the field, contractor safety is a driving factor in our safety performance. In 2023, the council focused on refining our contractor management plan and protocol to provide additional transparency on contractor performance and compliance with our requirements. We plan to continue maturing our contractor management protocol in 2024 to identify and work with contractors who have strong safety performance.
The council also rolled out our Life Saving Rules in a safety meeting in early 2023 and reinforced them by highlighting one of the ten rules during monthly safety meetings.
Council members and Devon safety leaders proactively engage with peer companies in our operating basins to improve company and industry performance in safety, public policy, the environment and other key areas. Devon is a member of the AXPC Health and Safety Subcommittee. At the AXPC Safety Symposium in 2023, the Devon CEO, vice president of EHS and measurement, and safety team members represented the company in discussions about industry safety. Devon continued our longtime sponsorship of the OSHA Oil and Gas Safety and Environmental Conference in 2023. A Devon health and safety leader was a founder of the conference and one of our EHS supervisors is an active member of the event’s advisory board. We’re also a member of the Onshore Safety Alliance (OSA), a voluntary industry coalition committed to reducing SIFs in U.S. onshore oil and natural gas operations.
In 2024, the safety team will work toward meeting a higher corporate safety performance goal and heighten the emphasis on health and safety performance through increased communications and performance reviews with Devon leaders. As part of this effort, our executive committee will review trends from SIF investigations throughout the year. We also have ongoing projects to incorporate safety data with operational data to improve our overall safety performance.
Building on our positive EHS culture
Encouraging a strong EHS culture at Devon is a priority for the EHS Council and the broader organization. We believe that the care and concern we show our workforce can have a positive impact on their safety and health at work and at home. We’ve learned from our field leaders that transparent communications, positive safety behaviors, proactive reporting and safely meeting operational goals are both signs and outcomes of a healthy EHS culture. The council assesses our EHS culture regularly to identify the most effective approaches and programs to foster strong safety performance.
We begin instilling our safety culture on an employee’s first day on the job. During new-hire orientation, they learn the safety behaviors we expect and incorporate into the employee appraisal process: visible commitment, accountability, anticipation, participation, recognition and communication. We keep the safety conversation and engagement going throughout their career.
Job competency is one of our EHS guiding principles, and we emphasize the quality of safety training over the quantity. A combination of online and hands-on training is offered to office and field workers based on their job responsibilities. All employees and contractors must complete our field safety briefing if they work on or visit field locations. Contractors also must complete our Devon Orientation through Veriforce, our third-party contractor performance network. Our training reinforces our requirement to immediately report any incident or near-miss event and to be accountable for our own and others’ safety.
To foster our positive EHS culture and behaviors, our Safe Work Award Program (SWAP) recognizes and rewards proactive reporting of workplace hazards and instances where work was stopped due to the identification of a safety concern. Both employees and contractors are eligible, and awards are presented at monthly safety meetings. Additional awards are given on a quarterly basis for the ‘best of the best.’ Good environmental catches became eligible for SWAP in 2023. In addition, our drilling, completions and workover teams recognize good stops by our contractors each month across all our operating areas. In 2023, 168 employees received SWAP monetary awards and 211 contractors were recognized with Devon branded items like coolers.
Engaging our workforce
Our Hearts & Minds workshops have been a core element of our safety engagement efforts with service, rig and contract drilling crews and leaders across Devon since 2014. During the workshops, we share our safety culture and approach to effective communication, continuous improvement, integrity and situational awareness to reduce safety risk.
We adapt the content to meet the needs of our workforce and business. In recent years, this led us to initiate honest discussions about mental health and tools to address mental health issues, including Devon’s Employee Assistance Program and suicide prevention and crisis hotline information. Hearts & Minds continues to be a place to talk openly about challenges and listen to our workforce as we drive home why safety is so important to Devon.
Roughly 60% of the 636 Hearts & Minds attendees across Devon in 2023 were contractors. To reach and engage even more people, the Delaware Basin team piloted Hearts & Minds workshops for specific categories of service providers with the highest risk/highest exposure.
Stop Work Responsibility
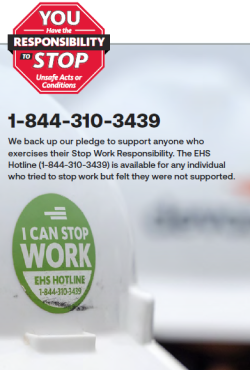
Proactively managing safety risks is a key factor in maintaining safe working conditions. Starting with new-hire safety orientation and continuing on our work sites, we emphasize the importance of Stop Work Responsibility. Employees have the right, responsibility and obligation to speak up and stop any action, task or behavior that is or could be unsafe. It’s also a way we live our value of courage, and Devon pledges to support anyone who exercises their Stop Work Responsibility. We capture and track proactive stops and good catches, and recognize individuals for stopping work to safeguard themselves, each other and the environment.
Contractor relationships
The contract vendors who provide work in the field are vital to safe, environmentally responsible and efficient operations, and building relationships with them to succeed as one team is a Devon value. We seek to work with contractors who have the strongest safety programs and track records, and we strive to work only with approved contractors who complete our supplier qualification process and meet our substantial policy and insurance requirements. Contractors are responsible for having EHS programs that meet or exceed all federal, state and local laws, rules and regulations, as well as Devon’s standards and protocols for essential safety activities.
As part of our supplier risk assessment process, we use Veriforce for third-party contractor verification and management. Our Veriforce dashboard allows us to monitor a contractor’s compliance with our EHS, insurance, OSHA verification, ESG and other requirements, and enables contractors to upload needed documentation. In addition, we use a separate third-party service to monitor contractors’ compliance with our drug and alcohol policy.
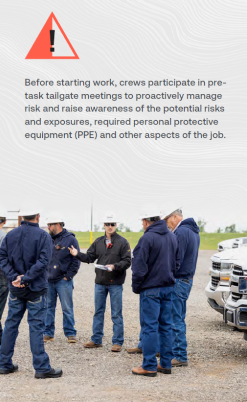
We require contractors to perform high-quality, safe and environmentally sound work. Contractors are expected to provide and retain quality personnel who are adequately trained to perform their jobs safely. Devon works constantly to raise the level of contractor safety performance through training and engagement.
Contractors must complete the widely used SafeLand, RigPass or equivalent safety training to work with Devon, unless specifically exempted by our EHS Contractor Management practice. These programs and Devon’s contractor safety orientation are available on the Veriforce eLearning platform. This orientation reviews critical safety rules for specific activities performed on field locations, such as fall protection, confined space, hot work, energy isolation, spill prevention and waste management. Oil haulers and all other contractors who work in transportation must complete safety briefings specific to their work. Devon’s company website provides contractors with easy access to our safety requirements, expectations, protocols, Safety Data Sheets (SDS), forms and tools.
We evaluate contractor compliance with the requirements to work on Devon locations. Our operations teams can review the evaluation results daily on our intranet to help them choose appropriate contractors for their needs.
Leadership engagements in the field can have a positive impact on our workforce, safety performance and operational excellence. Our field personnel wear hard hat stickers that say “Ask me my reason for working safely” to encourage safety-related engagements. The conversations that result often reveal that people work safely so they can return home to their family and friends — a higher motivation than simply following procedures.
To continue building relationships with contractors, our field safety professionals work with each of our business units to select contract companies to audit. The goal of the audit is to identify opportunities for EHS performance improvement. Safety professionals reviewed contractor EHS programs, made field visits and interviewed contractor crews to ensure their understanding and alignment of these programs in 2023. If issues were found, they developed action plans to help bring contractors up to standard. These audits helped us strengthen our relationships with our contractors, so we’re conducting even more audits in 2024 than in 2023.
In addition, we plan to continue hosting meetings with contractors who provide like services to discuss safety trends and our expectations. Meetings with electrical contractors in the Delaware Basin and roustabout providers in South Texas in 2023 helped strengthen our shared commitment to creating a safe work environment.
Auditing field and process compliance
Audits to identify and correct safety concerns are an element of Devon’s EHS Management System. Each business unit is required to perform an annual safety self-audit of compliance with regulations and our EHS protocols. Findings of noncompliance and suggestions for improvement are recorded in our Incident Management System (IMS) and tracked to closure. Business unit EHS professionals lead the audits, with guest auditors from other business units on hand to share best practices and lessons learned.
More than half of the audit time is spent at field locations, focusing on sites where work is under way so auditors can engage employees and contractors. Auditors check training, competency and inspection records and other documentation. We share trends observed and lessons learned during audits across the company to drive improvement.
Devon’s internal audit team provides an additional layer of review by performing operational audits in our field offices to examine processes and controls for supply chain, inventory, fleet management and other functions. Internal audit periodically assesses the field audit process and recommends improvement opportunities.
Audits also led to streamlining to one toll-free number for ethics, EHS and other issues across all Devon locations. Over time, the corrective actions we complete to address audit findings can lead to safety, operational and process improvements.
Committed to improvement
Devon sets annual corporate safety goals to focus our efforts to improve performance. Our emphasis is on preventing serious injuries and fatalities (SIFs) so our employees and contractors can return home safely every day.
We did not meet our safety performance goals in 2023, recording increases in both our overall injury rate and our SIF recordable rate. A contractor fatality at a rig in North Dakota deeply affected the rig crew and Devon employees alike. To help the team address their grief, our emergency management staff engaged the nonprofit Warrior’s Rest to provide counseling resources on location and one-on-one sessions.
Devon investigates every SIF event. EHS professionals conduct an investigation and utilize the TapRoot platform to determine root causes and corrective actions. After the investigation is complete, it is presented to business and EHS leadership and shared across the company. In 2023, we identified SIF root causes and assigned a wide range of corrective actions, including incorporating critical controls identified in SIF reviews in our KPA checklists for high-risk areas of the business.
We use SIF learnings throughout Devon to prevent future occurrences. In 2023, we started distributing SIF Safety Bulletins to operations leaders that describe a SIF, the initial investigation findings, and actions and next steps. Our operations teams discuss the information with contractors working on our locations. We received feedback from our field teams that the bulletins are an effective, simple tool to spark a safety conversation with our employees and contractors before they start work.
We also review SIFs where no one was injured (potential or near miss) and industry SIFs to better understand trends, mitigations and best practices. As a founding participant in the Onshore Safety Alliance (OSA), Devon committed to support the OSA guiding principles, industry sharing and learning, and to carry out a Life Saving Actions program, risk assessments, incident investigations and other safety actions.
To give a comprehensive view of our safety performance, Devon also tracks the Days Away Restricted Rate (DART), Lost Time Incident Rate (LTIR) and Total Recordable Incident Rate (TRIR) for employees and contractors. In 2023, our TRIR (for employees + contractors) held flat compared to 2022 with a rate of 0.53 while the number of work hours increased by 33% year over year.
Driving is one of the most dangerous activities for Devon employees, who drove 18 million miles in 2023, up from 13.8 million in 2022. Our “Engage Your Mind, Then Drive” safe driving campaign encourages a prejob planning approach to driving to positively impact Devon employees, their families and communities. Devon requires employees who have assigned vehicles to take hands-on commentary driver training. Based on industry data on seatbelt use, we emphasized seatbelt use in our contractor training in 2023.
2024 corporate safety goals
Devon’s 2024 corporate safety goals continue our mission to protect the lives of our employees, contractors and communities. Based on our underlying metrics, the goals are weighted toward year-over-year improvement in our SIF rate, and demonstrate our level of commitment to safety and to delivering a superior safety culture.
Safety accounts for 15% of the overall corporate scorecard in 2024. SIF actuals represents the largest portion of the safety goal. Utilizing SIF learnings to reduce SIF exposure and events and improve processes, culture and workplace safety remains a companywide goal for the sixth year.
Guided by our values to always do what’s right, support each other and proactively manage risk, we continue to empower the entire Devon team with the culture, tools and processes to work safely.