Air Emissions
Targets, technology and transparency
Devon is committed to reducing the carbon intensity of our operations, evaluating new opportunities and transparently reporting our results. We’re doing our part to be a responsible operator for the benefit of the environment, our employees and their families, our communities, our shareholders and our business— today and in the future.
Our long-standing commitment to reduce air emissions, particularly GHGs, is embedded in our culture through our Environment, Health and Safety (EHS) Philosophy and our core values to earn stakeholder trust, proactively manage risk and challenge ourselves to continuously improve. To reduce our impacts on the air and climate, we collaborate within and outside the company to implement technology, best practices and tools, and to generate new ideas and innovate.
Reducing the carbon intensity of our operations starts with proactively controlling and reducing air emissions from our operations. Devon focuses on reducing operational emissions of GHGs such as carbon dioxide (CO2) and methane, as well as volatile organic compounds (VOC), nitrogen oxide (NOx), sulfur oxide (SOx) and other gases, and reporting our results. In June 2021, we announced aggressive targets to lower the carbon intensity of our operations and outlined our approach to managing climate-related risks and opportunities in Climate Change Assessment Reports in 2021 and 2023. We’re taking these actions to lower our regulatory, market and reputational risk, but also because we believe protecting air quality aligns with our values and makes our business more sustainable.
Air emissions performance management
We invest in the latest equipment and deploy well-trained employees and contractors to carry out our emissions reduction programs. Our air quality program supports efficient, effective work by defining responsibilities and requirements for communications, compliance, recordkeeping and training.
Because emissions programs and results are critical to Devon’s overall performance, we’re organized to drive progress. Our vice president of EHS and measurement serves on the cross-functional EHS Council, providing continuity and alignment while elevating our companywide focus on ESG performance, including air emissions. To implement Devon’s emissions reduction strategy effectively, the EHS Council sets the strategy in close coordination with the vice president for EHS and measurement, sustainability team and senior leaders. In early 2023, we established our sustainability and external affairs team, led by the new role of director of sustainability and external affairs, to provide advisory support across Devon to help achieve our ESG and sustainability-related objectives and goals.
In addition, our sustainability and external affairs team closely monitors regulatory and legislative developments to understand the potential impacts to our operations and environmental performance. For example, we monitored the development and finalization of the EPA’s methane regulations and are developing execution plans for compliance. We anticipate that complying with the regulations will result in continued emissions reduction for Devon and the broader industry.
Investing in these resources reinforces the importance of meeting our targets and shows the level of leadership buy-in to continue our progress. It has also encouraged and enabled our business units to take ownership and operationalize their goals. Business units are devoting capital and resources to mitigate emissions, evaluate and enhance facility designs, and learn about the new technologies we may use to achieve Devon’s emissions goals.
Managing air permitting compliance
Compliance with all applicable federal and state environmental laws and regulations is central to our EHS Philosophy and the Devon Code of Business Conduct and Ethics. Our compliance process guides employees on meeting Devon’s air permitting requirements in our operating areas, aided by a web-enabled database that quickly distributes requirements for new and modified air permits to the people directly responsible for compliance.
Devon facilities and equipment may at times emit VOCs, NOx, SOx and other gases that are subject to state and federal emissions authorization permits and limits. We pursue full compliance by clearly communicating requirements to our operating facilities. Some facilities are subject to annual emissions inventories, which we submit to the appropriate regulatory agencies. The information is publicly available in states where these inventories are required. If compliance issues arise, we work expeditiously and constructively with regulators to address them. We’ll continue to proactively look beyond compliance to further reduce our air emissions.
Greenhouse gas emissions methodology
Devon reports GHG emissions from fuel combustion, flaring, fugitive emissions, venting and storage tank losses (Scope 1) and electricity consumption (location-based Scope 2) for assets under our operational control. We collect data on GHGs (carbon dioxide (CO2), methane and nitrous oxide) and submit annual GHG emissions according to the requirements of the EPA Greenhouse Gas Reporting Program. We also report indirect emissions from the use of sold products (Scope 3) on an equity basis from sources not owned or controlled by Devon. Scope 3 GHG emissions include indirect emissions from the consumption and use of Devon’s crude oil and natural gas production.
To estimate our Scope 3 emissions, Devon relies on Ipieca’s 2016 guidance document, Estimating Petroleum Industry Value Chain (Scope 3) Greenhouse Gas Emissions. According to this guidance, category 11, “Use of Sold Products,” is generally the largest contributor of Scope 3 emissions for a fuel-producing company and can account for more than 80% of a company’s total Scope 3 emissions. We report “Use of Sold Products” by calculating combustion emissions for our oil, natural gas and marketed natural gas liquids products.
It is important to note that Scope 3 emissions estimates are subject to uncertainty, inconsistency and duplication due to the reporting of assets outside the control of the reporting company and various reporting methodologies. In addition, two or more companies will account for the same emissions within their Scope 1, 2 or 3 emission inventories (as further described in the Ipieca guidance document).
As an exploration and production company, Devon has no direct control over how the raw materials we produce and sell are ultimately consumed. For this reason, we are committed to and focused on Scope 1 and Scope 2 location-based emissions for assets under our control, where we can most directly and meaningfully effect emissions reductions. We will continue to evaluate ways in which we can reduce value chain emissions and engage constructively with stakeholders upstream and downstream of our production operations.
Our baseline recalculation methodology
This baseline serves as a hypothetical reference point for what the emissions intensity would have been in the absence of emissions reduction efforts over time. To comparably track progress toward the targets, adjustments to the emissions baseline may be necessary to reflect structural, organizational or reporting changes that may occur over time. For example, an acquisition or divestiture could significantly impact our emissions performance and impair comparability from the emissions baseline.
We relied upon guidance from the Greenhouse Gas Protocol and Ipieca in establishing our baseline recalculation methodology. Our baseline will be adjusted if impacted by one or more trigger events that result in a change to the emissions baseline of 5% or higher on an absolute or intensity basis. Trigger events include structural changes; source ownership or control changes; changes to reporting boundaries, quantification methodologies or data improvements; or discovery of errors.
Our 2019 baseline has been recalculated to reflect the acquisition of Felix Energy in 2020, divestiture of the Barnett Shale in 2020, divestiture of the Wind River Basin in 2021, acquisition of RimRock Oil in 2022 and acquisition of Validus Energy in 2022.
We believe our recalculation methodology affirms our commitment to structurally drive down emissions, rather than divesting assets as a means to achieve our ambitious emissions reduction targets. We are committed to the ongoing review and assessment of the appropriateness of our emission reduction target levels and will adjust as needed.
GHG Emissions
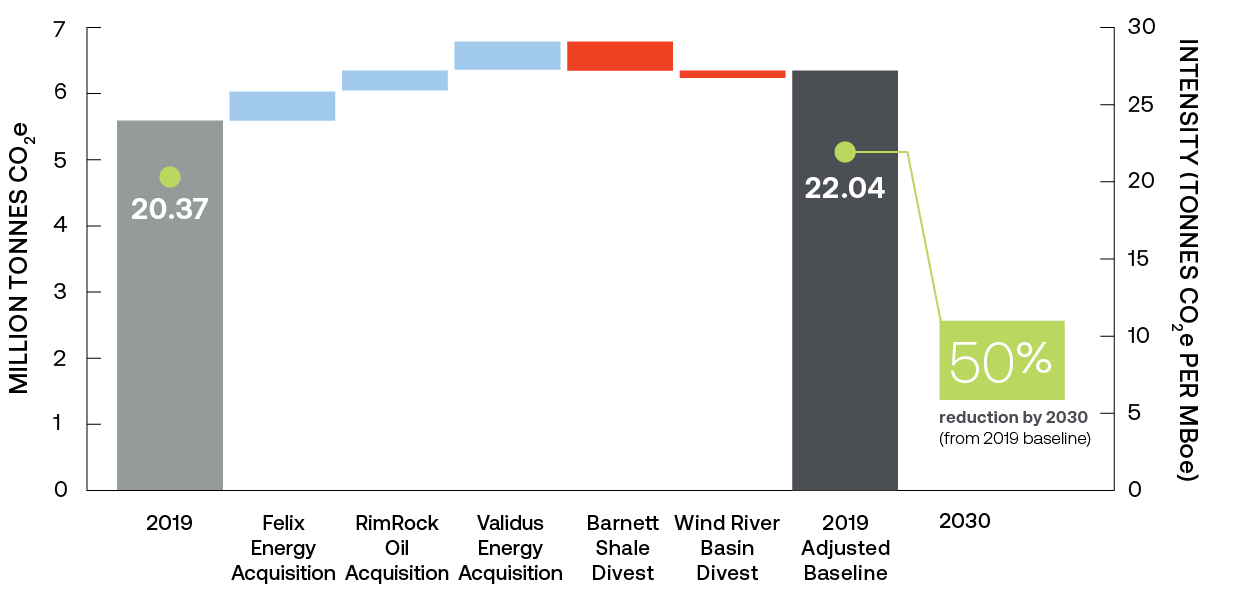
Methane Emissions
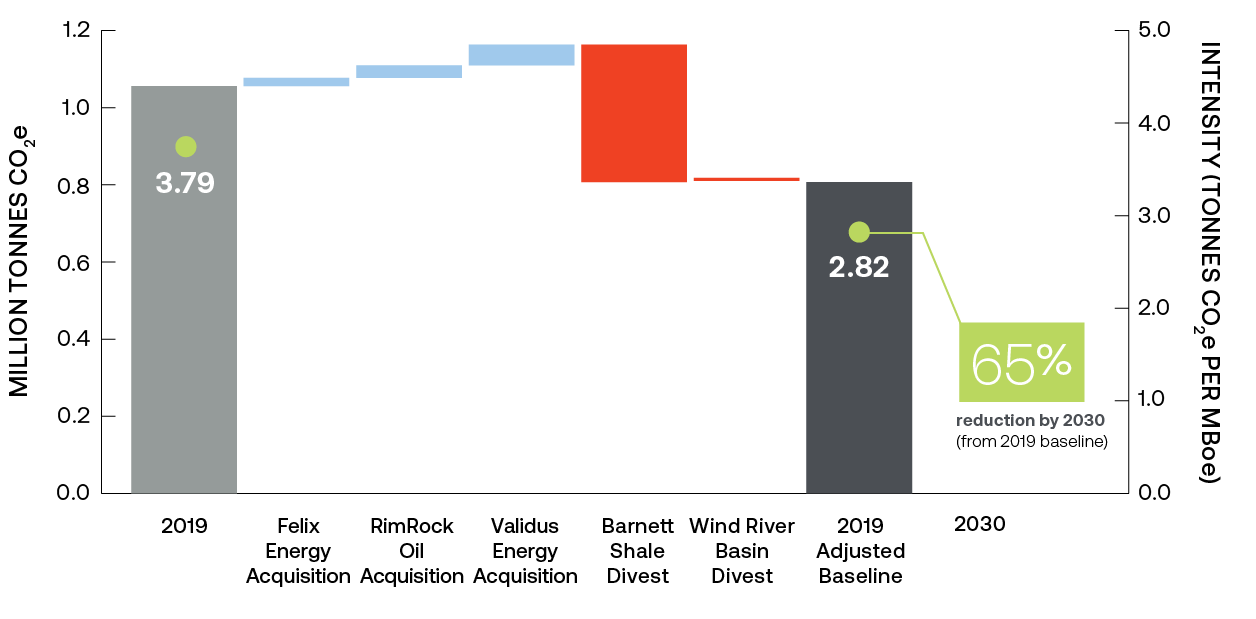
Addressing our primary emissions sources
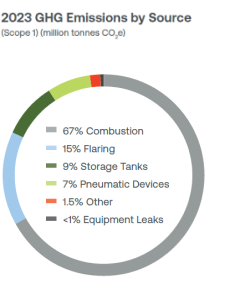
Our continuous improvement culture led Devon to develop a detailed understanding of where our emissions come from. This made it possible to address our air emissions at the primary sources through a variety of effective mitigation strategies:
- Reducing flaring across our entire portfolio of producing assets
- Expanding and enhancing our leak detection and repair program to find and fix equipment leaks
- Transitioning to air-driven pneumatic controllers
- Cutting combustion from drilling, completions and production by increasing the use of engines powered by electricity and alternative fuels
- Minimizing venting and flaring from storage tanks
We evaluate emissions detection and quantification on an ongoing basis and collaborate with industry, environmental groups and agency partners on emissions reduction strategies.
Flaring: Continuing reductions
Flaring of natural gas – a controlled ignition process for eliminating methane and VOC emissions – is necessary for safe operations in various phases of the oil and natural gas production process. Devon strives to avoid entirely the venting of raw gas and to limit flaring to the extent possible at all locations. Reducing flaring is a priority in our broader emissions reduction strategy because we want to protect the environment and capture as much natural gas as possible for its economic value, while also complying with laws, regulations and permits.
We continually evaluate and optimize our facilities, including installing reliable pressure-relief valves to minimize tank releases and vapor recovery equipment to capture flash gas emissions and route them to a pipeline. Devon also uses “green completions” to capture produced natural gas following hydraulic fracturing. Where flaring is unavoidable, we install pilot monitoring equipment to help ensure the gas is properly combusted.
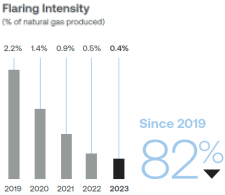
Flaring was once one of Devon’s highest emissions sources, but it is now one of our lowest emissions sources as a result of our commitment to prioritizing flaring reductions and employing best practices. The steep decline started in 2019, when we took a multipronged approach to reducing flaring at our Cotton Draw field, which accounted for most of our flared gas volumes in our Delaware Basin operations. As a result of our targeted efforts, flared volumes in our Delaware Basin operations in New Mexico and Texas declined from about 4% in 2019 to less than 0.4% in 2023. Setting our target in 2021 to lower our flaring intensity to 0.05% or lower by 2025 and eliminate flaring as defined by the World Bank by 2030 further spurred companywide improvements. By 2023, our flaring intensity had dropped to 0.4% compared to 2.2% in 2019 – an improvement of 82%.
We share our best practices with trade association partners because we believe it’s crucial that we work together to reduce flaring and air emissions across the industry. Devon is a founding member and current steering committee member of The Environmental Partnership, a voluntary coalition of oil and natural gas companies operating across the U.S. seeking to reduce air emissions. Devon chaired development of the partnership’s Flare Management Program launched in 2020. As part of the program, companies share best practices to reduce flaring, encourage beneficial use of associated gas, and improve flare reliability and efficiency when flaring does occur.
Devon continues to look at a broad spectrum of opportunities to reduce flaring and related emissions to not only meet our own targets, but continue improving performance across the industry.
Equipment leaks: Effectively reducing methane emissions over time
Methane emissions detection technologies are evolving rapidly and are a central component of Devon’s broader emissions reduction strategy.
Using optical gas imaging (OGI) cameras to detect leaks has been one of Devon’s primary emissions mitigation tactics since 2014. Our leak detection and repair (LDAR) program has been effective at finding equipment leaks from piping components and associated equipment and was a major contributor to achieving our first methane intensity target well ahead of schedule.
Environmental operators in each operating area focus primarily on conducting LDAR surveys at our sites and then making sure repairs are successful. We analyze the repair data to help us focus on reducing the number and frequency of leaks. If we pinpoint certain components or equipment that have repeat leaks, we consider replacing them on a field-wide basis. This approach led us to install thief hatches that have a lower leak rate and focus on specific equipment failures and settings. It also enabled us to improve flare maintenance and verify performance of vapor recovery units (VRU).
To help meet the regulatory requirements for LDAR inspections, our environmental and operations teams developed a mobile app to capture, enter, track and document LDAR survey findings. The app automatically syncs any needed repairs, all of which are required for compliance. This has resulted in a more efficient, consistent and systematic LDAR program.
We continue to learn from the LDAR data we collect and then refine best practices in facility design, equipment improvements and preventive maintenance to further reduce emissions from our facilities. For example, we conduct engineering and pre-startup reviews of facilities and take other steps to help verify design and proper installation of closed-vent systems and control devices.
To further reduce emissions from equipment leaks, we’re expanding and enhancing our LDAR program. In 2023, we continued building our program by:
- Surveying 2,781 production and well-pad facilities with OGI cameras at least once during the year (with some facilities surveyed more than once)
- Surveying 3,703 production and well-pad facilities with aircraft flyovers at least twice during the year, and
- Installing continuous emissions monitoring on over 200 of our production facilities
Devon has a cross-functional team that evaluates advanced methane detection technologies that have the potential to be effective at not only finding leaks more timely and over broader areas, but also assessing the magnitude of the leaks, allowing for faster detection, mitigation and quantification. We have investigated opportunities for advanced OGI, continuous onsite monitoring and remote detection using facility flyovers and satellites. At our emissions monitoring test facility in the Anadarko Basin, we tested multiple continuous, near-continuous and non-continuous technologies to identify viable innovative technologies for our operations. Based on our extensive evaluation and testing, in 2024 Devon began deploying perimeter-based and video methane emissions detection technologies broadly across our operating areas.
Through this technology assessment, we’ve acquired significant know-how and data that we are applying to our methane emissions reduction program. We’ve created a continuous monitoring dashboard, automated the work order process for repairing detected leaks and developed a methane monitoring interim standard operating procedure (SOP). Using lessons learned and applying best practices will amplify the impact of our methane emissions technology choices.
We will continue to monitor the rapid evolution of the technology solutions on the market, and identify, test and ultimately deploy the most promising technologies across our operating areas to help Devon reach our ambitious emissions reduction objectives and targets.
Pneumatic devices: Eliminating natural gas-driven devices
As part of Devon’s strategy to reduce our air emissions, we replaced high-bleed natural gas pneumatic controllers on hundreds of well sites in Wyoming, Oklahoma, New Mexico and Texas, and we no longer use them on new wells. In the Delaware Basin, legacy Devon has installed air-driven pneumatic pumps and controllers at nearly all new facilities since early 2019.
Combustion: Alternative fuels and power sources
Diesel motors powering drilling rigs and hydraulic fracturing operations can be a significant source of emissions. We’ve cut these emissions, reduced related noise and shrunk our operational footprint by replacing diesel-only engines with dual-fuel motors that run on diesel or compressed natural gas (CNG), liquefied natural gas (LNG), field gas or electricity. In 2023, about 27% of our wells were drilled with rigs running on dual-fuel or electricity. This avoided an estimated 11,700 metric tonnes of CO2 from 1.1 million gallons of diesel fuel.
Electrification is a key part of our strategy to meet our net zero GHG emissions for Scopes 1 and 2 by 2050. We seek to plan effectively so we can get grid power to our locations before drilling rigs arrive, when it is technically and economically feasible. Devon is also looking to identify other types of equipment and practices we can power with electricity in the future to avoid using diesel fuel.
In the Delaware Basin, we’re piloting an effort to supplement highly dynamic power demand by bringing emissions-reducing renewable energy and battery storage into our power supply. This effort involves integrating a behind-the-meter 5-megawatt solar array into our operations near the Texas-New Mexico state line area. The array will produce power that displaces electricity that would have been purchased from the grid and delivered across state lines.
To mitigate the challenges of electric power shortages in the New Mexico Delaware Basin, Devon is also investigating generating our own power with microgrids. By using natural gas from our operations to power turbines in an enclosed generation and distribution network, microgrids could reduce flaring and minimize our environmental footprint while also providing Devon with reliable power.
Ultimately, we expect the data generated from alternative power projects to help ensure the renewable energy is used efficiently, lowers costs and provides Devon a competitive advantage for future growth.
Storage tanks: Lowering venting and flaring
To reduce venting and flaring from oil and condensate storage tanks, we install vapor recovery towers (VRT) to maximize gas recovery and minimize the volume of tank vapors that need to be flared.
Devon standardized a low-emission storage tank design in the Delaware Basin following a successful pilot in 2021. The design further maximizes gas recovery and eliminates the need to flare tank vapors during normal operation. It also minimizes emissions by reducing the number of potential leak sources, as well as open thief hatches and other components that can lead to common equipment failures. We’re now expanding the low-emission storage tank design to all of our operations. In the Eagle Ford, we’re implementing a design that bypasses tanks and sends oil straight to pipelines to reduce venting and flaring from storage tanks.